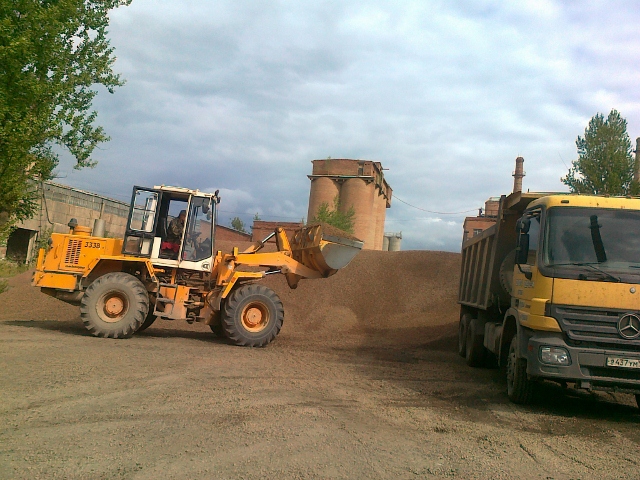
Свойства керамзита
Производство керамзитового гравия:
Мы производим керамзит путем двойного обжига глины, затем глина перемещается в специальный барабан. Этот металлический барабан вращается, во время вращения которого природный материал(глина) под воздействием центробежной силы превращается в гранулы, после чего обжигается во второй раз. Полный процесс производства керамзита читайте ниже.
Наш прочный, сверхлегкий и сверхтеплый материал (керамзит) производится по европейским стандартам. Здесь Вы можете посмотреть видео процесс производства керамзита.
Свойства керамзита:
Керамзит - морозоустойчивый и невосприимчивый к влаге материал, стойкий по отношению к щелочам и кислотам, прочный на сжатие, огнеупорность, химическую инертность, а также керамзит долговечен, так как не разлагается, не привлекает грызунов и различных насекомых, не подвержен гниению. Плотность керамзитового гравия от 350 до 700 кг кубический метр, прочность при сжатии от 0,4 до 6 Мн/м2 (3-60 кгс/см2), морозостойкость не менее 35 Мрз (35 циклов переменного замораживания и оттаивания), водопоглощение от 10 до 25%. Теплоизоляционные свойства керамзита определяются как средние – 0,10-0,16 Вт/м2К, но, несмотря на это, керамзит имеет хорошую звуко- и теплоизоляцию.
Технология производства керамзита:
Сущность технологического процесса производства дешевого керамзита заключается в том, чтобы обжечь глиняные гранулы по оптимальному режиму. Для того, чтобы глиняная гранула вспучилась необходимо, чтобы активное газовыделение совпало по времени с переходом глины в пиропластическое состояние. В нормальных условиях газообразование при обжиге глин происходит при более низких температурах, чем их пиропластическое размягчение. Поэтому при обжиге сырцовых гранул в производстве керамзина нужен быстрый подъем температуры, так как при медленном обжиге большая часть газов выходит из глины до ее размягчения, в результате чего получаются относительно плотные и маловспученные гранулы. Чтобы быстро нагреть гранулу до температуры вспучивания, необходимо ее высушить и подогреть.
Оптимальным режимом термообработки глины является ступенчатый режим по С.П. Онацкому: c постепенным нагревом сырцовых гранул до 200-600 °С и последующим быстрым нагревом до температуры вспучивания (около 1200 °С )
Обжиг глины для производства дешевого керамзита осуществляется в специальных вращающихся печах, которые представляют собой цилиндрические металлические барабаны длиной до 40-75 м, футерованные изнутри огнеупорным кирпичом. Печи медленно вращаются вокруг своей оси, их устанавливают с уклоном примерно 3 %. Поэтому сырцовые гранулы, подающиеся в верхний конец печи, при ее вращении, медленно передвигаются к другому концу барабана, где установлена форсунка для сжигания жидкого и газообразного топлива. Так, печь работает по принципу противотока: гранулы идут навстречу потоку горячих газов, подогреваются, затем, попав в зону воздействия огня форсунки, вспучиваются. В среднем, продолжительность времени пребывания сырцовых гранул в печи - около 40-45 минут.
Для обеспечения оптимального режима термообработки, зону вспучивания печи (примыкающую к форсунке) можно отделить от остальной части кольцевым порогом. Применяются также двухбарабанные печи - в них зоны подготовки и вспучивания представлены двумя сопряженными барабанами, вращающимися с разными скоростями.
Характер газовой среды в производстве керамзита обусловлен химическими реакциями, происходящими при обжиге. В восстановительной среде окись железа Fe2O3 переходит в закись FeO , что является главным фактором перехода глины в пиропластическое состояние. Восстановительная среда существует внутри гранул благодаря присутствию органических добавок, но при большом избытке воздуха в печи органические добавки и примеси могут преждевременно выгореть (возникает окислительная среда). Поэтому окислительная газовая среда считается нежелательной в стадии термообработки.
В восстановительной среде зоны вспучивания печи возможно оплавление поверхности гранул, вследствие чего газовая среда здесь должна быть слабоокислительной. Но при этом во вспучивающихся гранулах поддерживается восстановительная среда, которая поддерживает пиропластическое состояние массы и газовыделение, а поверхность гранул не оплавляется.
Характер газовой среды отражается и на цвете керамзита, в зависимости от состояния железных примесей: красноватая поверхность гранул достигается благодаря окислительной среде, темно-серая - благодаря восстановительной.
Выделяют 4 способа производства керамзита: пластический, порошково-пластический, сухой и мокрый (шликерный).
Самый распространенный - это пластический способ. Глинистое сырье в увлажненном состоянии перерабатывают в глиномешалках или других агрегатах , затем из получившейся глиномассы на ленточных шнековых прессах формируют сырцовые гранулы, которые при дальнейшей специальной обработке и транспортировке округляются.
Качество готового керамзита во многом зависит от качества самих гранул. В связи с этим нужна особо тщательная переработка глинистого сырья и формирование гранул одинакового размера. Величина гранулы определяется исходя из требуемой крупности керамзитового гравия и заданного для данного сырья коэффициента вспучивания.
Гранулы с 20%-ной влажностью могут сразу направляться во вращающуюся печь или предварительно подсушиваться в сушильных барабанах с использованием тепла отходящих дымовых газов вращающейся печи - что лучше повышает ее производительность.
Сухой способ- самый простой, используется при наличии камнеподобного глинистого сырья. Исходная порода должна быть однородной, иметь высокий коэффициент вспучивания и не включать в себя вредных включений - только тогда этот способ себя оправдает.
Технология такова: дробится сырье, затем направляется во вращающуюся печь. Перед этим целесообразно отсеять мелочь и крупные куски. (Крупные куски можно направить на дополнительное дробление)
Итак, производство керамзита по сухому способу легче, чем по пластическому, требует меньше капиталовложений, менее энергоемко, но, с другой стороны, по пластическому способу переработка глинистого сырья с разрушением его природного строения, гомогенизация, усреднение и возможность улучшения его примесями помогают увеличить коэффициент вспучивания. Экономичность этого способа производства обусловило тот факт, что сегодня даже в небольшой строительной фирме могут быть уверены, что по запросам «дешево куплю керамзит с доставкой» обязательно найдут выгодное предложение.
Отличие порошково-пластического способа от пластического в том, что сначала помолом сухого глинистого сырья получают порошок, а затем добавляют воду в этот порошок, и, получают пластичную глиномассу, из которой формуют гранулы так, как это было описано в пластическом способе. Требуются дополнительные затраты из-за необходимости помола. Также, если сырье недостаточно сухое, нужно его посушить перед помолом. Такой способ подготовки сырья подходит ко многим случаям : если необходимо ввести дополнительные примеси, то при помоле их гораздо легче равномерно распределить; если в сырье есть вредные включения гипса, зерен или известняка – в измельченном и распределенном по всему объему состоянии они уже не представляют опасности; если сырье по своему составу неоднородно - в порошкообразном состоянии его легче перемешать и гомогенизировать; если такая тщательная переработка сырья улучшает процесс вспучивания, то повышенный выход и более высокое качество керамзита оправдывают произведенные затраты.
Технология мокрого (шликерного) способа производства керамзита заключается в разведении глины в глиноболтушках (специальные большие емкости). Влажность получаемого шлама около 50 %. Пульпа насосами сначала подается в шламбассейны, а затем - во вращающиеся печи. В части вращающейся печи устраивается завеса из подвешенных цепей. Цепи нагреваются уходящими из печи газами и подсушивают пульпу, затем разбивают подсыхающую смесь на гранулы, которые округливаются, высыхают, нагреваются и вспучиваются - таким образом, цепи служат теплообменником. Такой способ рекомендуется использовать при высокой влажности глины, когда она выше формовочной (при пластическом формовании гранул). Также он применяется в сочетании с гидромеханизированной добычей глины и подачей ее на завод в виде пульпы по трубам. Достоинства этого способа - возможность тщательного распределения добавок, простота удаления из сырья зерен известняка и различных каменистых включений, а также достижение однородности сырьевой пульпы. Так как у шликера достаточно высокая начальная влажность, нужно расходовать большое количество топлива – это главный недостаток мокрого способа.
Полученный по любому из вышеперечисленных способов керамзит после обжига необходимо охладить. Прочностные свойства керамзита зависят от скорости охлаждения. При слишком медленном охлаждении керамзита из-за смятия размягченных зерен может снизиться его качество. С другой стороны, при слишком быстром охлаждении в гранулах керамзита могут сохраниться остаточные напряжения, которые могут проявиться в бетоне или же они могут растрескаться.
После вспучивания керамзита рекомендуется его сразу быстро охладить до температуры 800°С для того, чтобы предотвратить окисление железа и для закрепления структуры керамзита. Затем желательно медленное охлаждение керамзита до температуры 600°С в течение 20 минут для того, чтобы в ней формировались кристаллические минералы, которые повысят прочность керамзита, а также для обеспечения затвердевания стеклофазы без больших термических напряжений. Затем, в течение нескольких минут, возможно быстрое охлаждения керамзита.
Сначала керамзит охлаждается в пределах печи поступающим в нее воздухом, далее керамзит следует охладить воздухом в аэрожелобах, слоевых или барабанных холодильниках.
Чаще всего внутризаводским транспортом керамзита является конвейерный (ленточные транспортеры), редко – пневматический (поток воздуха по трубам), так как при пневматическом транспорте возможно повреждение поверхности зерен керамзита и их дробление.
Для того, чтобы фракционировать керамзитовые гранулы используют грохоты, чаще всего это барабанные – многогранные или цилиндрические. Затем, фракционированный керамзит поступает на склад готовой продукции силосного или бункерного типа, где ждет своего покупателя, который наверняка уже набирает в поисковой системе «дешево куплю керамзит от производителя»
В случае если керамзит используется для теплоизоляции грунта, надо учитывать его высокое водопоглощение (8 – 20%). Перед засыпкой керамзита на грунт, под бетонную стяжку, необходимо предварительно постелить полиэтилен. Керамзит – материал без вредных для здоровья веществ!
Характеристики керамзита:
Теплопроводность: 0,10-0,16 Вт/(м2К)
Удельный объем аккумуляции тепла: 1 000 Дж/(кг2К)
Диффузионное сопротивление водяному пару: 2-8
Класс строительного материала: А1 - негорючий
Объемная плотность: 300 — 700 кг/м3
Первичная энергетическая емкость: 300-450 кВт/м3
Химический состав глины:
SiO2 | Al2O3 | Fe2O3 | FeO | TiO2 | CaO | MgO | SiO3 | K2O3 | Na2O3 | п.п.п. | орг. |
61,7 | 17,3 | 4,6 | 2,2 | 0,7 | 1,1 | 1,5 | 0,1 | 2,6 | 0,9 | 6,0 | 2,23 |